Making Transformations Dance – Mastering the Operational Excellence Beat for 2025
Picture yourself in a DJ booth, adjusting the sound to shape the perfect atmosphere. The bass is thumping, lights are flashing, and the crowd is moving to the beat. In front of you is a massive mixing board, full of sliders and knobs. Each small adjustment changes the experience—if you turn up the bass, the floor vibrates. If you increase the treble, the details of the melody become clearer.
Operational excellence works the same way. Instead of one dramatic transformation, success comes from fine-tuning the right levers over time. As we step into 2025, we see four key trends gaining stronger focus. Companies are refining and evolving their approaches to meet today’s challenges, rather than abandoning what works.
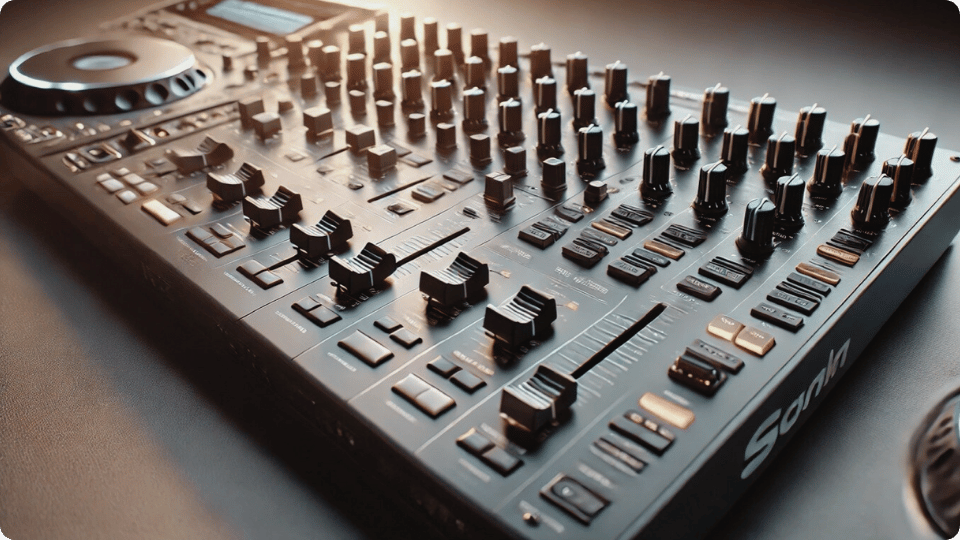
Slider 1: From Adopting Generic Concepts to Developing Unique Production Philosophies
Organizations have long adopted pre-packaged methodologies—Lean, Agile, Six Sigma—assuming they are plug-and-play solutions. Now, this trend is shifting even more clearly. Companies are no longer just “implementing Lean” but are crafting their own production philosophies with a stronger emphasis on sustainability and longevity. They want their operational models to be deeply embedded in their culture, ensuring long-term relevance and resilience. Organizations define what operational excellence means for them, adapting core principles to fit their unique challenges and strategic goals. It’s no longer about following a set script—it’s about writing their own to ensure their philosophy never disappears.
Slider 2: From Expert-Driven Transformation to Leader-Driven Transformation
The era of waiting for external consultants or internal specialists to “fix” operations is fading. Instead, leadership at all levels is stepping up. Companies are shifting their transformation strategies so that leaders—from top executives to frontline managers—actively own and drive change. When transformation is fully owned by leaders, lengthy pre-studies become unnecessary because they already understand their operations. This results in highly effective and sustainable transformations. The mindset is shifting: rather than depending on experts to drive change, companies are empowering leaders to take ownership. Internal experts still play a crucial role, but they act as personal trainers—guiding and coaching—while leaders must do the heavy lifting. Transformation is no longer seen as a project; it is a capability that leaders continuously develop and refine. When leaders lead transformation, change sticks.
Slider 3: From Tool-Driven Implementation to Principle-Focused Learning
Operational excellence is often mistaken for deploying new tools and methods, but true transformation happens when all leaders deeply understand the underlying principles. When leaders grasp these principles, they gain the flexibility to adapt them across different contexts, making transformation more dynamic and sustainable. In a rapidly evolving world where tools and methodologies constantly change, deep comprehension of principles is the true competitive advantage. In 2025, the focus is on teaching fundamental concepts—flow efficiency, problem-solving, and customer value—so employees and leaders can develop their own solutions rather than applying one-size-fits-all tools. The most successful companies won’t be those with the most advanced tools, but those where employees and leaders truly understand why and how to improve, ensuring long-term adaptability and resilience.
Slider 4: From Big-Bang Transformations to Small-Step, Continuous Change
Large-scale, top-down transformation programs are becoming obsolete. Instead, organizations are shifting toward small, incremental changes that compound over time. It’s not about winning a marathon; it’s about becoming a consistent jogger. The same applies to continuous improvement—success isn’t about executing one large-scale transformation initiative but about embedding a habit of systematically implementing small improvements.
To achieve this, companies are forming cross-functional and functional teams with razor-sharp goals. These teams systematically work over long periods to drive focused improvements with a clear mission. For example, one cross-functional team might focus on minimizing lead time in a certain end-to-end flow, while another is dedicated to delivering the best customer experience. The improvements remain small, but they are implemented continuously with a shared, intense focus.
This regular practice builds long-term resilience and competitiveness. Rather than attempting to redesign everything at once, companies are making constant, focused enhancements—quick experiments, fast feedback, and continuous learning. This slider shift makes organizations more adaptable and resilient, improving every day instead of waiting for the next big initiative.
Fine-Tuning for the Future
These four shifts aren’t about radical reinvention—they’re about fine-tuning the system to create sustainable, meaningful change. Organizations that adjust these sliders carefully will be the ones setting the pace in 2025.
So, as you begin 2025, ask yourself: Which levers are you adjusting in your operational excellence journey?